What is Flock?
Flock is technically tiny, short fibers (usually shorter than 6mm in length). They are cut to either precision lengths or random lengths. Flock can be synthetic or natural materials of various deniers (a unit of fineness for fibers). Since synthetic fibers can be made continuously, they are cut to precise lengths. The fibers are bundled by the millions and then cut with a guillotine-type device, in the exact length needed. By contrast, natural fibers are staple fibers and are cut randomly in rotary-type machines. Basically, any fiber can be cut into Flock. It could be cotton, rayon, acrylic, polyester, nylon, aramids and just about any type of fiber.
The Flocking Process?
Depending on what the desired end use is, fibers can be cut and finished in different ways to have specific properties. In the case of Flocking, the fibers are finished so as to sift well, and charge in an electrostatic field. This allows us to attach the fibers to various surfaces in a perpendicular direction, giving the finished product that characteristic, velvet-like feel. The fibers can also be dyed to any color needed, and dispersed into various products, like coatings or textured papers, or can be pasted onto surfaces.
What does the Adhesive do?
In order to be useful, flock has to stay put. To provide the world-class, ultra-useful product we make at Spectro Coating, flock must stay put on several very different surfaces. This can vary widely, based on whether it will be used for;
- An interior designer creating a unique, functional, personal look for a hotel.
- A craft materials company turning out custom ribbon or fabric.
- A high-tech firm looking for an amazing new filter, or…
- A medical company looking for a soft, durable and safe material.
The adhesive anchors the flock fibers to any kind of substrate, which could be an object, fabric, film, or any other type of rolled good. Using the correct adhesive is vital. Both the substrate and the final use must be considered. Desired characteristics that could influence the adhesive used include such things as whether the product will need to be rigid or flexible, flame retardant, or washable.
Also, the process by which the flock is adhered to the substrate could influence the materials used. But do not worry! The engineers in the Spectro Coating R&D lab have spent decades perfecting the science of bringing flock and substrate together. Whatever it is you need, we can do it.
What Kind of Adhesives do we use?
Adhesives can be solvent, or water based. There is some flexibility in the fine-tuning of the adhesive, but basically, it is like anything else in the world of flock; the manufacturing process used and characteristics of the end product desired will influence the makeup. As you know, Spectro Coating is an American company that puts the environment top on its list. We do our best to keep harsh chemicals in check. If you want to get technical, we only use water-based adhesives – mainly acrylic latex systems, but occasionally urethane and epoxy systems as well.
Getting it to Stick; How is the Adhesive Applied?
It probably will not shock you if I explain that the substrate and end product characteristics influence the adhesive application process. But that does not mean it is a simple dump & pump…We apply the adhesive is several ways; knife over roll, reverse coat, screen printing, or gravure (using etched plates or cylinders).
One common method of use is rotary screen printing. This allows us to “print” the adhesive in any pattern and then apply the flock. The flock then sticks to wherever the adhesive is, and any remaining unglued fiber is vacuumed off the substrate. Translation? Custom designs; everything from simple words, phrases, and graphics to incredibly intricate, beautiful patterns. You may have already seen some in high-quality furniture pieces or famous hotel windows and wall coverings.
The Final Steps
The after applying the adhesive the material is dried and cured in an oven. Then we brush and clean to remove any loose fibers. We wind the rolls, and they are ready for shipment.
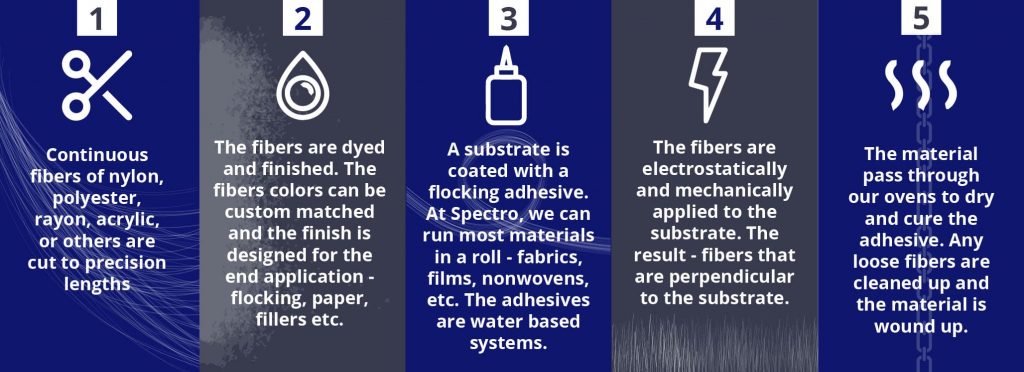